Characteristics of Rubber Wood
Rubberwood, also known as Hevea brasiliensis, is a type of hardwood derived from the Pará rubber tree. This versatile wood is widely used in various industries, including furniture manufacturing, flooring, and construction. Its popularity stems from a combination of unique characteristics that make it an attractive choice for many applications. In this article, we will explore the characteristics of rubber wood in detail, highlighting its properties, uses, and benefits.
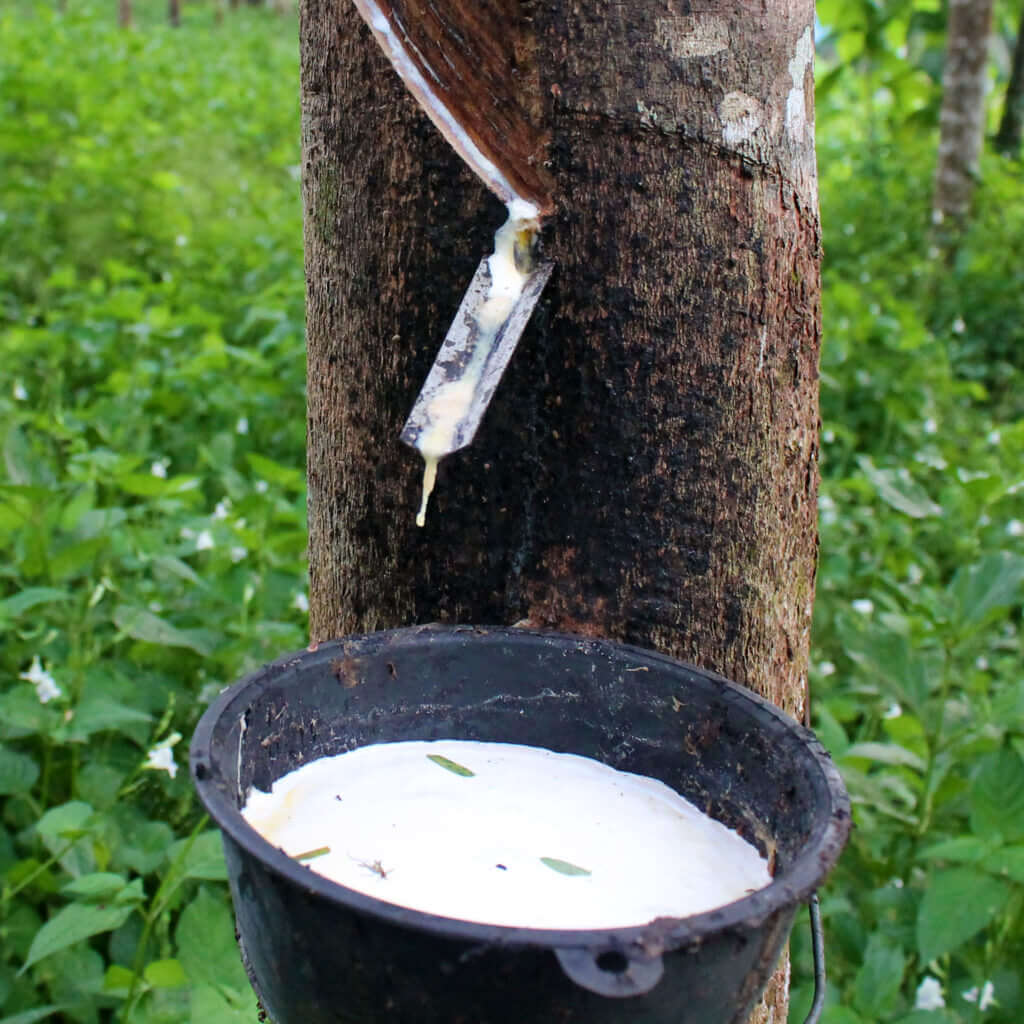
-
Color and Texture:
Discover the varied Characteristics of Rubber Wood in terms of color and texture. The wood can range from pale white to youthful chocolate, offering a smooth, uniform surface ideal for furniture and flooring. Its smooth texture and regular fiber pattern not only enhance visual appeal but also simplify processing and finishing.
-
Weight and Density:
Discover the Weight and Density Characteristics of Rubber Wood. Compared to hardwoods like teak or mahogany, rubber wood is relatively lightweight with lower density, facilitating easier cutting and shaping. Its low density makes it ideal for furniture requiring frequent adjustments. Despite its lightness, Rubber Wood remains robust enough for everyday use.
-
Durability and Resilience to Insects:
An important aspect of rubber wood is its moderate durability. Although not as strong as some other hard woods, rubber wood is long-lasting enough for use in various settings. However, without specific treatment, it may be more prone to insect attacks like termites. To increase resilience to insects and extend its lifespan, rubber wood is often treated with chemical protectors or preservation processes.
Mechanical Properties of Rubber Wood:
The mechanical properties of rubber wood determine its use and applications in various industries. The most important aspects include strength and flexibility, water absorption and release, as well as its behavior under load. Let’s discuss each of these aspects in more detail.
-
Strength and Flexibility:
Rubber wood is known for its extraordinary flexibility, allowing it to withstand deformation without breaking. Although not as strong as some hard woods, rubber wood is sufficient for most furniture and light construction applications. This flexibility is particularly beneficial in manufacturing items that require some flexibility, such as tool handles or certain furniture parts that may need to adapt to external pressure or use.
-
Water Absorption and Release:
One important characteristic of rubber wood is its ability to absorb and release water. Its hygroscopic properties allow rubber wood to expand and contract based on environmental humidity levels. While this can be seen as a weakness in certain applications, proper processing, such as suitable drying and finishing, can minimize negative effects. This treatment is important to ensure that the wood remains stable and maintains its form and size over time.
-
Behavior of Rubber Wood Under Load:
Under load, rubber wood demonstrates the ability to withstand burdens to a good extent, thanks to its unique fiber structure. However, due to its lower density compared to harder woods, rubber wood may not be ideal for applications requiring extreme strength or constant heavy loads. When designing and constructing with rubber wood, it’s important to consider this factor and use it appropriately according to its capabilities.
Processing and Utilization of Rubber Wood:
The processing of rubber wood involves several important stages to maximize its mechanical properties and expand its uses. Proper drying is key to reducing the risk of deformation or cracking due to changes in humidity. Additionally, surface treatments such as coating or using protectors can increase durability and resistance to water and insects.
The utilization of rubber wood is diverse, ranging from furniture making to flooring and components in automotive and toy industries. Its processing flexibility and diverse applications make rubber wood a valuable and versatile material.
Cutting and Drying Techniques:
The cutting and drying processes of rubber wood are important steps in preparing the raw material for various applications. Cutting techniques typically involve selecting appropriate trees, using saws or cutting machines, and processing to produce boards or beams with desired dimensions. Characteristics of Rubber Wood: After cutting, rubber wood must be dried carefully to reduce moisture content and prevent deformation or damage during use.
The Use of Rubber Wood in Furniture Making:
RubberWood has become a very popular material in the furniture-making industry due to its unique combination of natural beauty and practical mechanical properties. In furniture making, rubber wood is used to create various items such as tables, chairs, cupboards, and beds. Its ability to be carved, chiseled, and polished makes it an ideal material for furniture with various styles and designs.
Other Applications of Rubber Wood in the Construction and Decoration Sector:
In addition to furniture making, rubber wood is also widely used in the construction and decoration sectors. In construction, rubber wood is often used for floors, walls, and ceilings. In decoration, it is used for making wall panels, windows, doors, and other decorative accessories. Characteristics of Rubber Wood: Due to its beauty and ability to be carved, rubber wood is often chosen for decorative projects that require intricate details.
Sustainability and Environmental Aspects:
In terms of sustainability and environmental considerations, rubber wood offers benefits as it can be replanted after harvesting. Compared to the use of harder woods, which may not be sustainable, the use of rubber wood can help reduce pressure on forests. However, it’s important to note that responsible forest management practices are essential to ensure the long-term sustainability of the rubber wood industry.